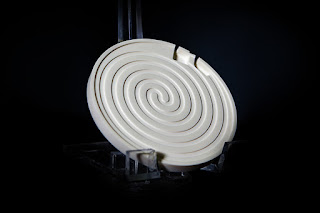 |
Ceramic heating element |
Manufacturers of laboratory and process analytical equipment, as well as medical equipment, are continually challenged to make products smaller and more compact. Smaller, more efficient components are always in demand. Providing heat for sample stability or a chemical reaction is a common requirement. There's an ongoing challenge to find smaller and more efficient
electric heaters.
Many traditional electrical heating elements are limited in size and efficiency due to the balance required between conductor temperatures and the the heat transfer properties of the dielectric material used in their construction. Sometimes the mass required to insulate electrically is at odds with the ability to drive the heat into the part. Metal sheathed heaters use compacted magnesium oxide, or wafers of mica for dielectric. While these provide good electrical insulation, they also inhibit thermal transfer from resistance element to the external part. Flexible heating elements use a variety of rubbers or fluoropolymer elastomers that sandwich the resistance element. While these designs are dielectrically strong, and allow for excellent heat transfer, they are limited by the maximum operating temperatures and watt densities of the elastomer.
A newer, alternative technology is
“thick-film” ceramic heaters, a process of depositing a resistor “trace” of tungsten paste on top of a ceramic part in a process very similar to screen printing. The deposition process allows for close control of thickness and width of the resistor, thus accurately controlling the conductor resistance, wattage, watt density, and uniformity of the heated part.
The use of ceramics as the heater body (referred to as a heated part), has many advantages. Ceramics are chemical inert, offer excellent thermal conductivity, impervious to moisture, and are very durable. The downside to using ceramics as heaters, however, is the difficulty in machining to very tight tolerances. In recent years though, many of the ceramic machining hurdles have been overcome through
advanced ceramic machining processes.
In the early years of development
thick-film ceramic heaters had a few major challenges. Dealing with mis-matched expansion coefficients between the ceramic substrate and the conductor trace was considerable. Years of research now have yielded excellent data on compatible materials making this problem much less significant. Another challenge is controlling the tolerance and repeatability of the heater resistance from part-to-part. Improvements and advancement in this area are made possible with laser etching, tighter screening procedures, and advanced machining.
The use of ceramics provided many interesting possibilities in heater design, and many materials were tested and researched. The most common ceramics used for thick-film heaters today are alumina (Al2O3), silicon nitride (Si3N4), beryllium oxide (BeO), and aluminum nitride (AlN). Each material has its own unique chemical and physical properties, but all exhibit good thermal conductivity and good dielectric properties.
The combination of excellent thermal conductivity, high dielectric, high watt densities, precise thermal profiling, and custom shapes and sizes that make thick-film ceramic heaters so attractive to equipment manufacturers. Providing more heat in smaller areas is easier than with traditional heaters. Additionally, some of the ceramics used are non-contaminating and moisture-proof, making them excellent candidates for clean and ultra-clean applications.
Ceramic thick-film heaters have many advantages over metal or elastomer sheathed heaters beyond just providing a more compact component. They are very fast acting, durable, moisture proof, and contamination proof. They can be designed and machined to virtually any size or shape, watt density, voltage, and distributed wattage profile. While the initial design and prototyping requires investment in time and money, the resulting product can be mass produced economically and with repeatable accuracy and quality.
For more information, contact:
BCE
(510) 274-1990
www.belilove.com